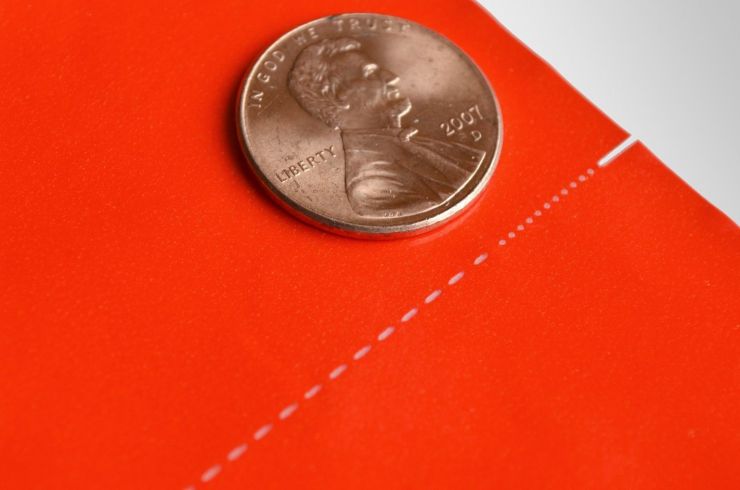
By John Dillon, Vice President-Marketing; and Jim Bucklew, Senior Applications Development Engineer, Preco Inc.
Abstract
The market for prepackaged produce continues to grow at a brisk pace. This growth is a result of a market desire for the convenience of pre-packaged foods that minimize meal preparation time. Packaging technology plays a key role in the ability of food suppliers to offer case-ready products, specifically the ability to offer flexible-packaging films that are tailored to match the vapor transmission rate of the specific food product to maximize its shelf life. A key technology that controls the vapor transmission rate is the use of industrial lasers to micro-perforate the flexible-packaging material. This article investigates the current state-of-the-art and recent improvements in laser micro-perforation of flexible-packaging materials and looks at future technologies and trends that could improve this process.
Micro-Perforated Flexible-Packaging Film
Flexible-packaging technology plays a key role in optimizing produce shelf life and in the overall quality of the food product while reducing spoilage in the supply chain. “Basically, the right packaging coupled with the right storage temperature can help create conditions in the packaging that will delay maturation and aging of produce. Therefore, it is possible to increase shelf life and/or to harvest the product later so the product is sold with better quality. Packaging really can make a difference. If both temperature and packaging are optimum, aging of produce can be slowed down more than 800 percent." [1] With these obvious advantages, it is clear why micro-perforating of flexible packaging in this market has grown.
Controlling the transmission of oxygen, carbon dioxide, ethylene and water vapors through the flexible package for each specific produce is important, as the optimum storage conditions vary according to the product type, processing and ripening degree, time of harvest and more. Because the transmission rate for the gases and vapors varies, it is not economical or technically feasible to produce a flexible-packaging film for each food product. It is far more economical to produce families of films that can then be laser-altered to yield the desired transmission rate. In this manner, cost-effective lot quantities of film can be produced, and the film then can be tailored for the product to be packaged. The questions then become, how is the transmission rate altered and what technique provides the highest-quality film for the food supply chain?
Table 1 illustrates the difference in micro-perforations required, depending on the product being packaged. Both packages are for 6-oz servings, but melon requires three times the oxygen transmission rate (OTR) versus citrus. This is accomplished by placing four micro-perforations on the lid for the melon and two for the citrus.
It should be noted that, in addition to laser micro-perforating, there are two other perforating processes for flexible packaging: Needle and electrostatic perforating. However, as laser micro-perforating technology has advanced, the laser’s ability to produce consistently round holes to an optimized size has become the dominant production process for micro-perforating flexible packaging. As such, this article will focus discussion on laser micro-perforating.
Laser Micro-Perforating
Using lasers for micro-perforating various materials has been possible for decades. While not an early application, laser micro-perforating is now a well-established process in the flexible-packaging market (see Figure 1).
Laser improvements have been impressive, however, the pulse on-time duration compared to the distance the web travels during this time still needs to be factored into the micro-perforating process. With a stationary web, the laser can be rapidly pulsed (100-µsecond pulse duration) to produce a consistent round hole, but as the web ramps up to a high speed at 1000 fpm (300 mpm), even this short pulse length will result in an elongated hole that is not acceptable (see Figure 2).
To solve this problem, it is important to have the laser beam track the web – regardless of web speed – so as to produce holes to specification. The ability to accurately track the web with the laser beam is accomplished by placing a scanner device in the optical beam path. The scan rate is determined by an encoder that monitors web speed and allows the laser pulse to track the web at the same velocity. This solution is programmable and allows consistent hole perforations to be placed – regardless of web speed – so that even during web ramp-up and ramp-down, this configuration produces micro-perforations within specification.
With this base configuration, a laser that exhibits rapid rise and fall times with high peak-power capabilities, along with a scanner controlled by encoder feedback from the web velocity, can place consistently round holes of 0.004 in. (100 microns) in diameter. The holes may vary ±0.001 in. (±25 micron), but this is within the range required to produce the required OTR. Maintaining the same hole diameter – regardless of the product being packaged – minimizes setup time, as only the number of perforations in the package is varied to match the vapor transmission rate required for the food product.
Systems Overview
Micro-perforating systems: A micro-perforating system is composed of a number of discrete subsystems (see Figure 3). The first subsystem is a web-handling arrangement that can range from a wide-web slitter/rewinder to a rewinder-type system. The web system must provide a smooth and controlled ramp-up and ramp-down of the web speed, in addition to good web-guiding capabilities. The second subsystem is the laser modules that are integrated to the web-handling subsystem. It is important to note the laser modules can be integrated to existing web handling setups, or they can be supplied as a complete integrated arrangement.
When specifying requirements it is important to know how many rows of perforations are needed, as this will determine the number of laser heads required. It is important to understand that all micro-perforating for extended shelf life is performed in the machine direction and not across the web width. The reason for this is a fundamental optics issue. Simply stated, to produce a 0.004-in. (100-micron) diameter hole in film, a focused spot size that is slightly less than the hole size is required. There is a direct relation between the focused spot size and the focal length of the lens being used. To produce the relatively small 0.004-in. (100-micron) diameter hole, a short focal length lens is needed. This works well for machine-direction perforating, but if crossweb micro-perforating is required, a much longer focal length lens would be necessary to scan the web width, and the resulting hole would be much larger and not suitable for this market. The laser module consists of a laser that is properly sized for the worst-case film construction, a scanner-based motion system that allows the focused laser beam to track the web during the time it takes to produce the perforation, and the motion- control system to control the laser parameters and perforation rates. The process of laser-beam tracking the web during the laser pulse-on cycle is referred to commonly as “beam compression,” which allows a round perforation to be produced. The motion-control system requires a number of inputs, such as a rotary encoder that provides input on web speed and also a registration sensor that allows the perforation schedule to be triggered from a printed eye-mark. The required number of laser-focusing heads are then mounted to the slide rails so that each head can be traversed across the web to a specific location that requires perforation.
Making the Operation Economical
Lasers have a high initial cost, so it is important to have a strategy for their effective use. While the laser module approach, which has one laser to one scanner/focusing assembly and offers advantages, an alternative and more cost-effective approach
is to use a single laser and optically split the laser beam. The incremental increase in cost for a higher power laser is much less than for a second laser; however, two optical considerations need to be addressed. A primary specification requires consistent and identical hole diameters, so it is important to engineer a system that assures this.
There are two issues to address. The first is making sure the laser beam is split 50/50 so that each focusing optic is passing the same energy. If this split is not maintained, the side with more energy will produce a larger hole. Advances in optic-coating technology have greatly increased the consistency of beam splitters, to the point where there is less than 2 percent variation in the output beams. That level of power variation will not cause a difference in measured hole size between the split beams. The other issue to address is the incoming beam diameter. All laser beams slowly diverge as they exit the laser cavity. With the split- beam approach, the distance of one focusing head to the other will be different, resulting in a different beam diameter on the focusing optic, which can yield different hole sizes. Using good optical engineering practices, the laser beam can be up-collimated and optically manipulated to produce a consistent beam diameter through the range of motion of both focusing heads, resulting in consistent hole diameters from each head. The result is consistent hole diameters regardless of the crossweb position of the two focusing heads, while reducing the overall cost of the system.
Technology Improvements
Technology that improves hole consistency has evolved over the years. It is important for the flexible-packaging converter to be assured the hole size remains consistent throughout the production run and that each package has the correct number of holes.
Laser pulse monitoring: Closed-loop power control now is being used to confirm that the laser has produced the correct number of programmed micro-perforations. This is a technological advancement for the micro-perforating process. In the event a pulse (or a series of pulses) is not detected by a feedback sensor (closed loop control), that information is forwarded to the machine control where it is compared to preprogrammed limits. If a missed-pulse limit is exceeded, the machine will initiate a controlled stop. This feature is critical, as the shelf life of the product requires the correct number of micro-perforations per package. Monitoring and confirming the laser pulse to produce the micro-perforation is an excellent quality assurance step for the converter.
Laser power control: The closed-loop power control used for laser-pulse monitoring has an additional benefit. While this article's primary focus is micro-perforating flexible packaging, this same system can be used for machine-direction scoring to produce easy-opening features for the package. By altering the laser parameters, the system easily can be transitioned to this process. A key requirement of scoring is controlling score depth.
Controlling Inconsistency
CO2 lasers exhibit two primary forms of inconsistency that need to be controlled (see Figure 4). The first is long-term, naturally occurring power fluctuations of +/-5 percent to 7 percent, which can have an effect on score depth. The other is a variation that occurs at laser startup as a result of the laser warming up to operating temperature. The closed-loop power control feature maintains a constant laser-output power and ensures a consistent score depth throughout the production run. This allows the laser power to be increased or decreased to maintain laser-power stability less than 2 percent of the programmed setpoint.
Future Advancements
Currently, technology advancements in laser micro-perforating have been incremental rather than revolutionary, resulting in market stability. Additionally, advances have focused on ancillary technology, such as laser power control, laser-pulse confirmation and in-line video inspection. At present, laser micro-perforating can match the web speed of slitter/rewinder systems, and although the initial cost of laser perforators is high, their maintenance and operating costs are relatively low.
The current CO2 laser technology is well suited for micro-perforating flexible packaging. Sealed, diffusion, cooled lasers have been on the market for decades. These lasers exhibit high pulse energies as a result of fast rise and fall times, on the order of 40 microseconds. These lasers also have a fairly low dollar/ watt ratio, making them an attractive choice for this market.
Alternative laser technologies would need to produce much higher pulse energies in a much shorter pulse length to eliminate the need for beam-compression optics, thus simplifying the system. A review of the laser resonator market indicates there are two lasers that may meet this objective. A quick overview of each follows:
Q-switched CO2 – Q-switched lasers have a long history in the Nd:YAG laser market and are now commercially available with CO2 lasers. Q-switching involves placing an EO (electro-optic) gating device in the beam path where the EO device can reflect the laser beam back into the laser resonator, greatly increasing the stored laser energy. The advantage to this offering is the high peak power and very short pulse length this laser can produce. [2] While these lasers are worth investigating to understand their capabilities, the reality is a beam-compression system will still be required, so the advantage of pursuing this option is minimal. There is a potential marginal improvement for more money due to the laser cost.
Ultra-fast lasers – Relatively new to the industrial laser market are ultra-fast lasers that exhibit incredibly short pulse lengths in the nanosecond and picosecond range. This technology produces high peak energies at very short pulse lengths, but at a high frequency. This technology is being deployed to cut the glass faces of smartphones and to drill high-aspect, small-diameter holes into fuel injectors. [3] At this point, very little work has been done in the flexible-packaging market due to the high cost of ultra-fast lasers. While the potential exists to eliminate beam compression, this cost savings does not compensate for the high cost of the laser itself.
Conclusion
The current technology and system offerings for laser micro- perforation of flexible-packaging materials are well established, stable and accepted. Current systems offer a means to produce the specified micro-perforations at the required intervals and matching the web speeds of current slitter/rewinders. Technology improvements would require either improved performance or a reduction in equipment cost. At present, any alternative laser technology would result in only nominal performance improvement, but at a much higher price, which would not be cost-effective. While the technologists might be disappointed, the business owner can be confident in making an investment decision and not having a new system become obsolete in the near future. ◼
References
- Danish Technological Institute, "Packaging and Transport," 2008.
- Lee, Stephen, "Q-switched CO2 lasers deliver power," Industrial Laser Solutions, June 200
- "Drilling of High Aspect Ratio Holes with Picosecond Lasers," White Paper, Coherent, Inc.
John Dillon, Vice President-Marketing for Preco, Inc. (Somerset, WI), has more than 25 years of experience in the industrial laser market. His past work includes selling industrial lasers and custom laser systems for Coherent General, AB Lasers and Laser Machining, Inc. In 1998, John was a founder of LasX Industries, Inc., and worked there until 2012. He can be reached at 715-247- 3285, ext. 1109, email: jdillon@precoinc.com
Jim Bucklew, senior applications development engineer at Preco, Inc., has 28 years of laser-applications development experience and has been a key contributor in the development of laser applications for micro-perforating and scoring flexible-packaging materials. He can be reached at 800-775-2737, email: jbucklew@precoinc.com
Used with permission of CONVERTING QUARTERLY, Peterson Publications, Inc. Copyright (C) 2014 Q4.